Press
Swiss Precision Since 1961
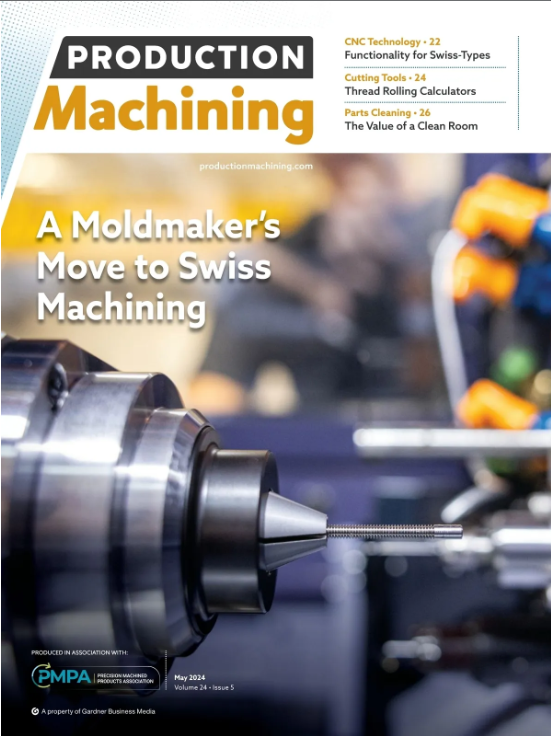
Heule's SOLO-L Featured In Production Machining
In the June 2024 issue of Production Machining, Heule's SOLO-L tool is spotlighted for its robust capabilities in spot facing and counterboring, suitable for diameters from 25.0 to 45.0 mm. Titled "Heule Spot Facing, Counterboring Tool Provides Flexible Machining," the article showcases the tool's ability to handle tough materials like nickel and titanium. It features a straightforward, reliable design without the need for anti-rotation devices or spindle rotation changes, with a sealed system to prevent coolant contamination. The SOLO-L's customizable options and series-wide versatility highlight Heule's commitment to precision and efficiency in manufacturing.
Read the full article in Production Machining's June 2024 issue.
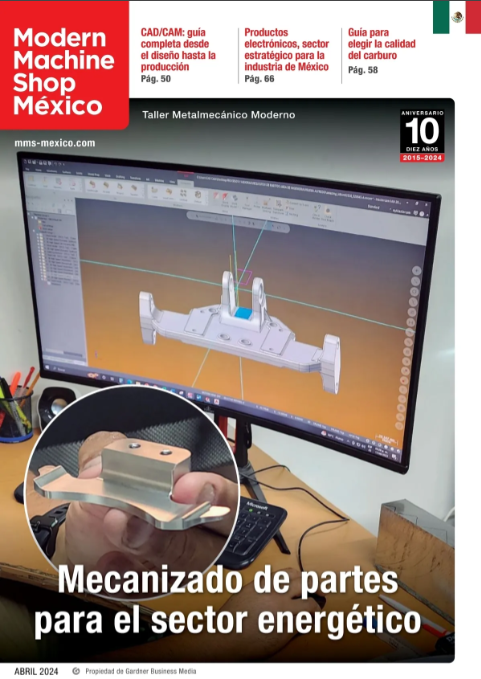
Heule BSF Manual Featured In MMS & MMS Mexico
HEULE Precision Tools was featured in "Modern Machine Shop" and "Modern Machine Shop Mexico" for their manually actuated BSF tool, designed to handle back spot facing where coolant flow is too weak to actuate the blade. Highlighted for its ability to work in environments without a reliable air supply, the BSF manual is ideal for large boring mills and outdoor machinery. It simplifies the machining process by operating without anti-rotation devices or spindle direction changes, significantly cutting operational costs and enhancing reliability in difficult-to-reach areas. This feature underscores HEULE's commitment to innovation and addressing industry-specific challenges.
Read the full article in Modern Machine Shop April 2024 or MMS Mexico April 2024 issue.
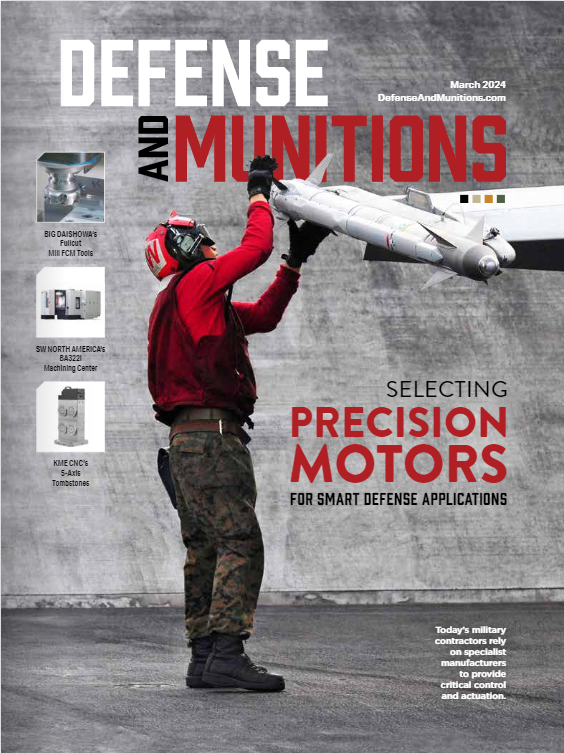
Heule Introduces The BSF Manual
HEULE was recently featured in "Defense and Munitions," where they introduced their innovative manually actuated BSF tool for back spotfacing. This tool is a game changer for settings where coolant flow is too weak and air supply is inconsistent or unavailable. The BSF manual allows for manual retraction and deployment of the blade, making it ideal for challenging environments such as large boring mills and open-air machines. Its capability to handle counterbores up to 2.3 times the diameter of the through-hole, alongside its availability in standard and custom sizes, positions it as a versatile and essential tool in various industries, including aerospace and automotive.
Read the full article in Defense and Munitions March 2024 issue.

Solving a Cross-Bore Deburring Issue
HEULE worked with the car manufacturer to create a product that would suit its needs. The first proposed sollutions had a large control housing that the manufacturer didn't have the space for in its facility. HEULE went back to the drawing board and came back to the manufacturer with the COFA-X, a revision of its COFA tool designed especially for cross-bore deburring.
After months of testing and communications back and forth, the car manufacturer commissioned HEULE to repeat in its production plant the successes it had in the development laboratory. By the third run, the automated deburring process was corrected and optimized to perform the task without error.
Learn about Heule's solution for cross-bore deburring
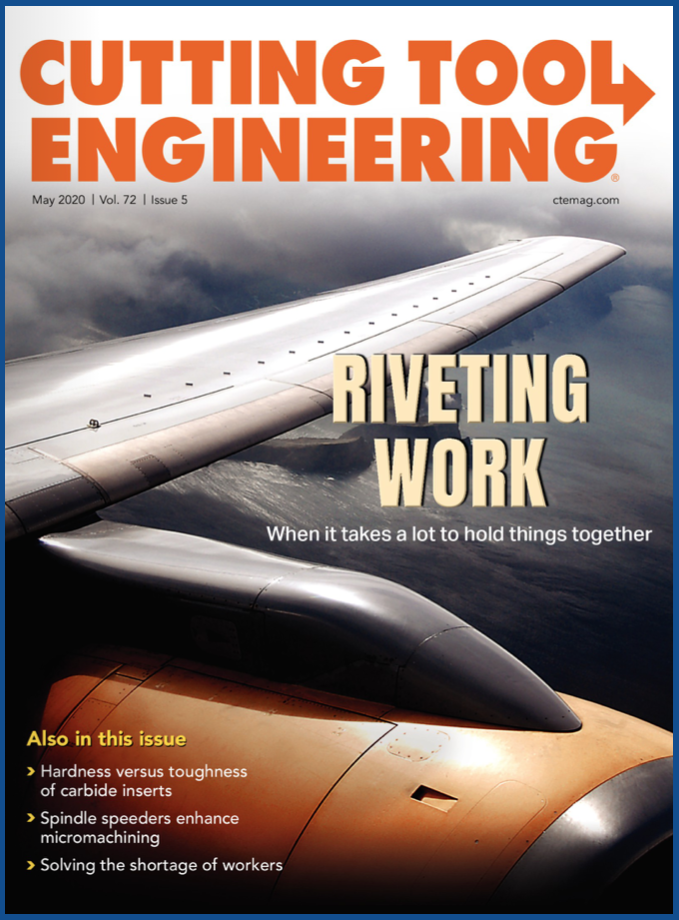
Fastened for Flight
Automation is increasingly prevalent in aircraft manufacturing, HEULE President Gary Brown said. System providers continue to develop ways to streamline the holemaking process, using robots and tracked “crawlers” to reduce the need for humans in what has long been the most labor-intensive step of fuselage production.
“You have companies like Boeing and Airbus employing 40,000 workers with air guns to deburr and chamfer and countersink millions upon millions of holes each year,” he said. “So it’s only logical that they want to automate this wherever possible, not only to reduce costs but, more importantly, to improve product quality.”
Discover efficient techniques for deburring machined edges
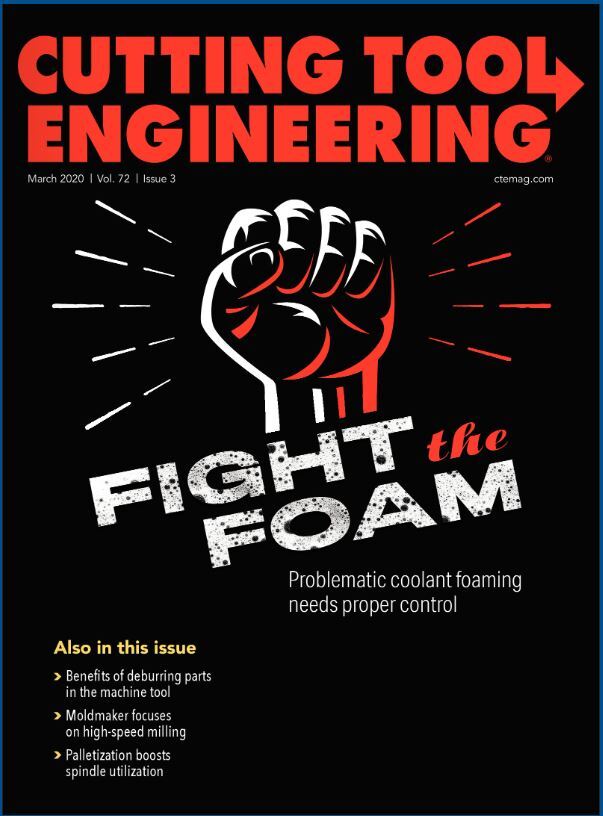
How to eliminate machining saddle burrs
Just as holemaking is common in metalworking, so is deburring the tops and bottoms of produced holes. Chamfering tools are effective, as are the familiar Rotoburr-style scraper blades. These tools also deburr machined edges fairly well and, given the right extension or blade geometry, can access hard-to-reach areas deep inside parts. Add a few Scotch-Brite pads, a drill press and a bench grinder to the mix, and there’s little that any skilled machine operator can’t deburr.
However, these traditional deburring methods are slow. Features that can’t be reached while in a machine — which is often much of a part — must be manually scraped, buffed and chamfered. If an operator isn’t paying attention, a machine tool might sit idly while he or she is busy deburring parts. And a bit too much pressure with a grinding wheel or blade could mean the inadvertent scrapping of a completed, possibly very expensive machined component.
Optimize your deburring process with these tips
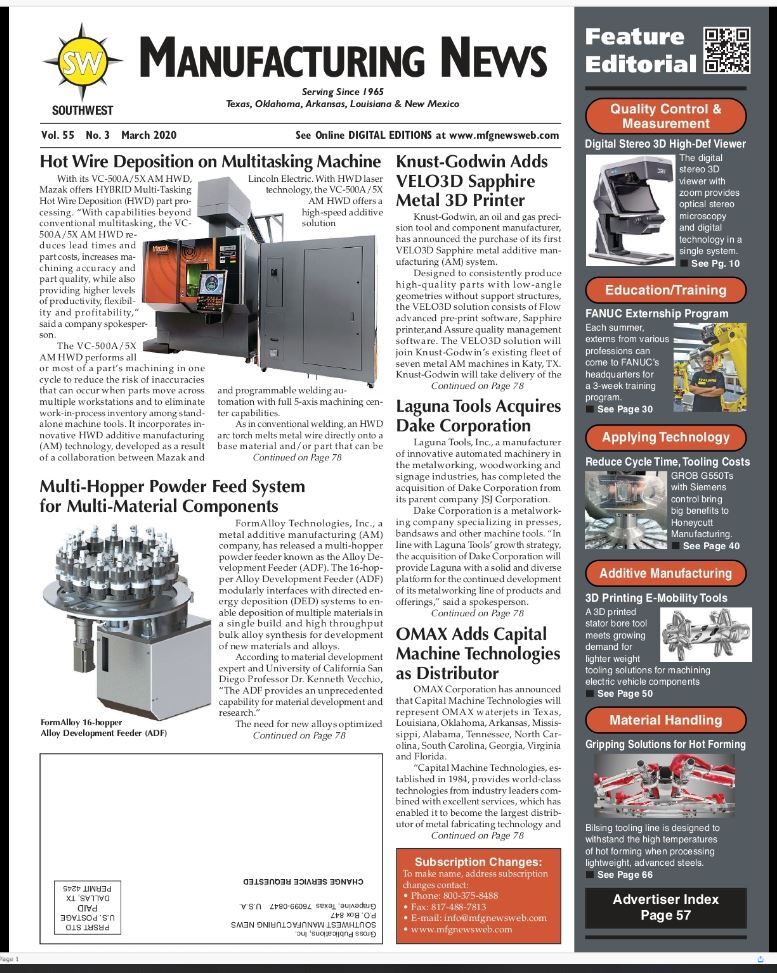
Put the Right Tool in a Multi-Tool Manufacturing Line
The Heule SNAP tool provides this multi-tool manufacturer more chamfering and deburring, and does it faster than deburring by hand, preventing sluggishness and downtime due to maintenance or repairs. “Whether worn on a belt loop or stashed in a toolbox, we try to put the right tools into the hands of our customers,” said the manufacturing engineer. “By adding Heule Tool’s SNAP chamfering tool, our production line has the right tool
for the job as well.”
Enhance your multi-tool manufacturing line with Heule's SNAP tool
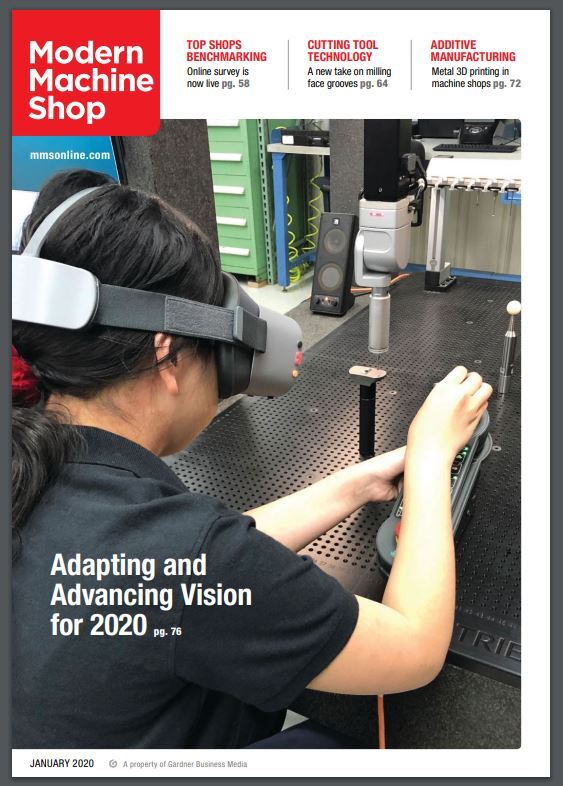
Drilling and Chamfering Tool Solves a Vexing Problem
Like many manufacturers, Houston-based Utex Industries had a vexing problem: how to save time on the production line while maintaining the quality and consistency of its product. The company manufactures polymeric seals, custom urethane and rubber molding, and well service products for the fluid sealing industry. Any inconsistency in the product, such as a burr left on a chamfered hole, can lead to critical part failure. One product that Utex makes has a collar on the seal cap to prevent leaking. The part is made of aluminum bronze and has eight to 10 holes through the outer- and inner-diameter walls on each part. The shop’s adoption of a couple of Heule’s Snap 5 Vex-S tools for its Okuma lathes have met the dual goals of efficiency and consistency.
Ensure quality and prevent part failure with Heule's Snap 5 Vex-S chamfering tool
.png)
Overcoming a Back Spot Facing Challenge
Whitcraft Group Machinists use Heule Tools to meet tight tolerances on difficult Inconel parts.
Aerospace industry specs often call for a part to be machined to the thousandth of an inch. In an ideal world, that level of precision wouldn’t sacrifice production time or tool longevity. Whitcraft Group, a manufacturer of aerospace components, is living in that ideal world, machining parts accurately, quickly, and without tool failure.
Mike Anderson, lead/supervisor of the Bearing Housing Flow Line at Whitcraft, gives the credit to the back spot facing (BSF) tool from Heule Tool he recently brought into the shop’s line. The BSF has sped up production time, decreased insert costs, and increased tool longevity, without sacrificing precision.
Achieve precision and efficiency with Heule's Back Spot Facing (BSF) tool
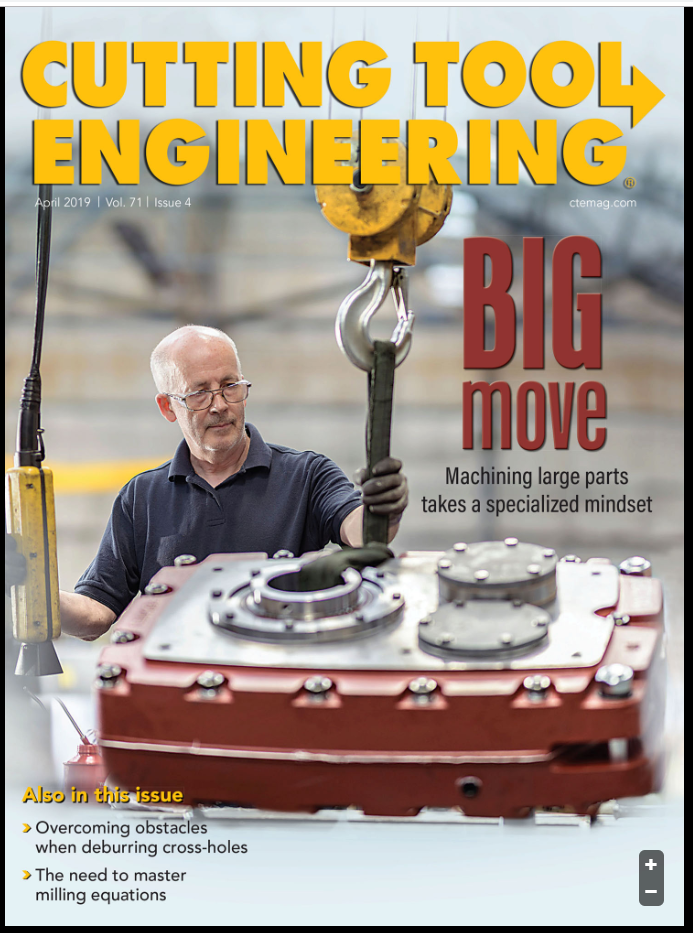
Crossed Up
Specialized tools help deburr cross-holes.
Deburring drilled holes is essential to the manufacturing process. Burrs that aren't cleaned up can cause part failure by breaking off and clogging or damaging a part or an assembly or by cutting a wire or an O-ring that's passed through a bore. But cross-holes, where two or more holes intersect, are hard to reach and often require deburring by hand.
Learn how specialized tools can efficiently deburr cross-holes
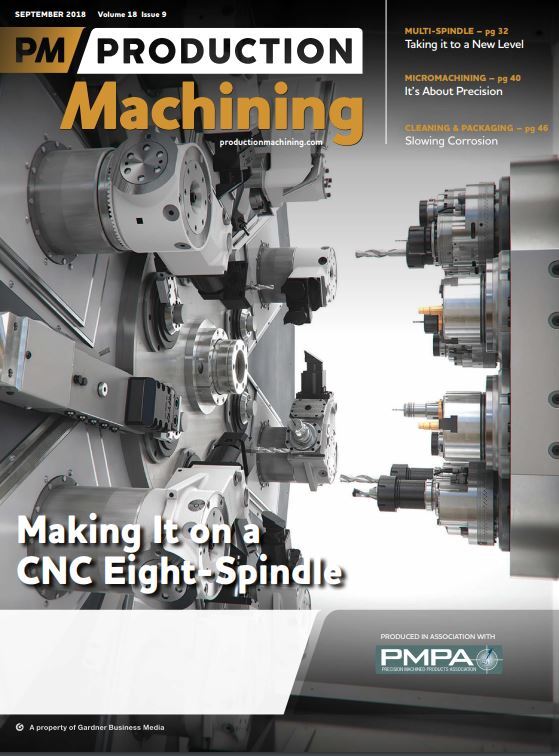
Automated Deburring Tool Increases Production of Subsea Valves
Multiple difficult-to-reach holes, each of varying sizes, and of varying quantity depending on the part in question made machining subsea valves at Abco Subsea difficult. But ever since the company found the Cofa C Series tooling from HEULE Tool, it has worked flawlessly in the production line.
Efficiently machine subsea valves with Heule's Cofa C Series
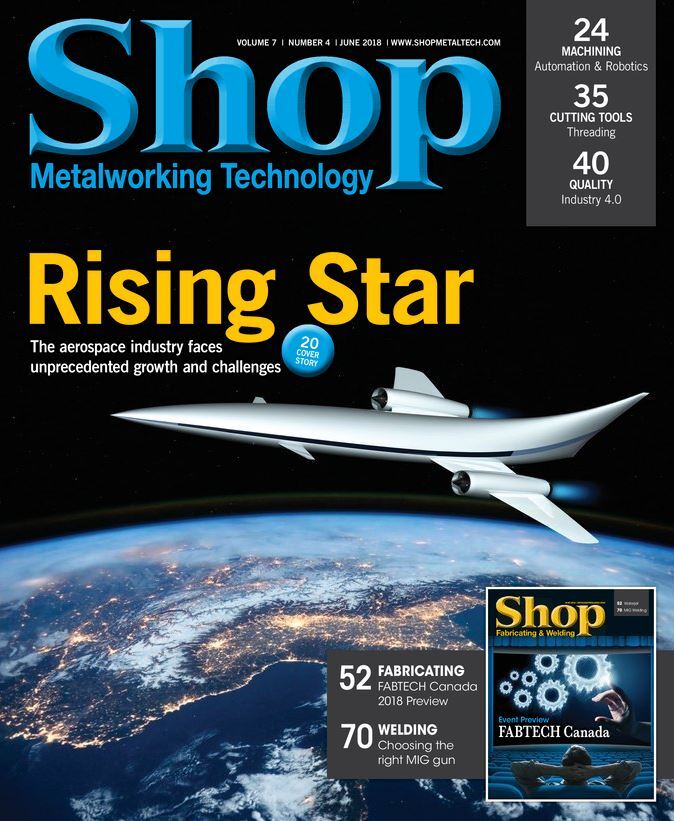
Deburring Cross-Hole Intersections with Automated Tools
by Gary Brown
Machinists and programmers alike know how demanding cross-hole drilling can be, as it often exacerbates many of the difficulties inherent in metalworking.
Deburring is already a painstaking process, but when burrs are difficult to inspect and access, as is the case in cross-hole intersections, traditional deburring methods are time consuming and inefficient.
Improve productivity with automated deburring tools for cross-hole intersections
.jpg)
Macro Economics, Micro Burrs: Get a Handle on Cost per Part, Set a Target
The mindset that should accompany decision making about how best to deburr parts should depend on establishing a target for cost per part. That’s the sage advice of LaRoux Gillespie, Dr. Eng, FSME, CMfgE, PE, a past president of SME and author of 13 books on burrs and deburring.
Learn from industry expert LaRoux Gillespie about cost-effective deburring strategies

Back Spotfacing Tool Frees Production from Costly Bottlenecks
Automating a time-consuming, intricate process can save a shop time and money while freeing up labor power for other tasks. Sometimes automation looks like a robot or a computer; but sometimes it looks like a counterboring tool with a retracting blade. A back spotfacer from Heule Tool (Loveland, Ohio) removed the need for operators at one machining business to manually detach and reattach the tool’s cutting head, reducing process time by two to three hours per part, on average.
Experience time and cost savings with a back spotfacing tool

Driving Automatics:
Automatic back spotfacing frees manpower at Vancouver machine shop
For Sicom Industries, reliability and on-time production are what keep their customers coming back. Its parts are high value and its clients are in competitive industries, so being successful sometimes comes down to having the right tool for incredibly specific jobs, like back spotfacing up to 40 holes in an intricate casting for an oil pipeline.
Enhance production reliability with automatic back spotfacing
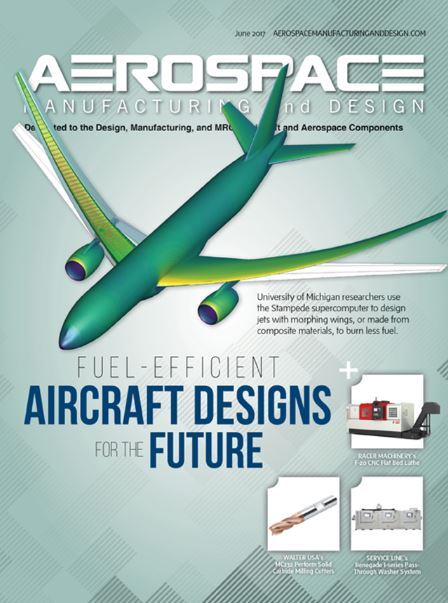
Precise Through-Holes
Implementing the right tools helps achieve perfectly deburred chamfered through-holes – and these tools benefit more than just jet engine manufacturers.
Gary Brown, vice president and general manager, Heule Tool of North America, explains that currently, "A major jet engine component manufacturer uses the Heule-BRM tool combination for finishing chamfered holes on rotating engine parts.
"They do this, not only because it is an efficient way to achieve the very stringent tolerances required, but also because there simply is not another method of doing the work that is sufficiently stable and repeatable."
Learn more about deburring solutions for jet engine components

Cutting back spotfacing cycle time
Fulflo Specialties Inc used the HEULE SOLO tool to increase productivity
“Machining time on the valve bottoms, which includes boring the hole to size, drilling and back spotfacing, dropped from 39 minutes to 15,” Collett said. “And that’s running at the low end of the recommended speed and feed range for the back spotfacing tools.”
Tool life increase was equally impressive. “So far we’ve run 420 stainless valves, up from 2 on the old tool and we’ve only indexed the two-sided inserts once,” Collett reported.
Boost productivity with the Heule SOLO tool
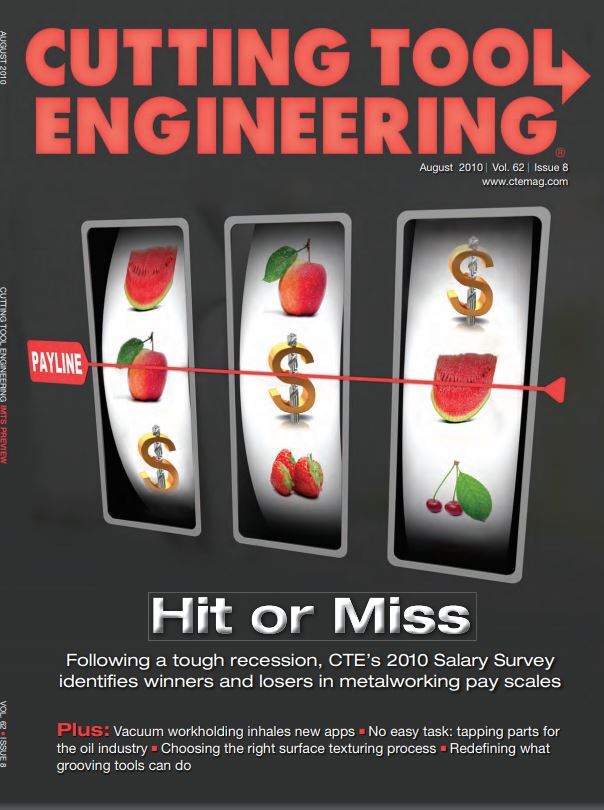
Smooth Flight
A set of tools is used to automate drilling, reaming, deburring, and edge blending of chamfered through-holes for jet-engine fasteners.
To avoid delays and reduce tool costs, some aerospace manufacturers are automating holemaking and finishing processes that incorporate cutting, edgebreaking and deburring tools as well as ball-style flexible hones for the edge blending process. Some jet-engine manufacturers are recommending or requiring that suppliers use these automated processes. One such combination uses Heule’s DEFA chamfering tool, its COFA universal deburring tool and a miniature Flex-Hone tool from Brush Research Manufacturing Co. Inc. (BRM), Los Angeles.
Discover the benefits of Heule and BRM tools for aerospace manufacturing