Reducing Labor Applying Spotfaces to a Nickel Chain Wheel Drum
Challenge:
A contract manufacturer was looking for a solution to apply back spotfaces for the bolting that does the job without the time-consuming re-clamping of the work piece. The time used for the re-clamping amounted to approximately 1 hour per work piece (not including alignment and zeroing).
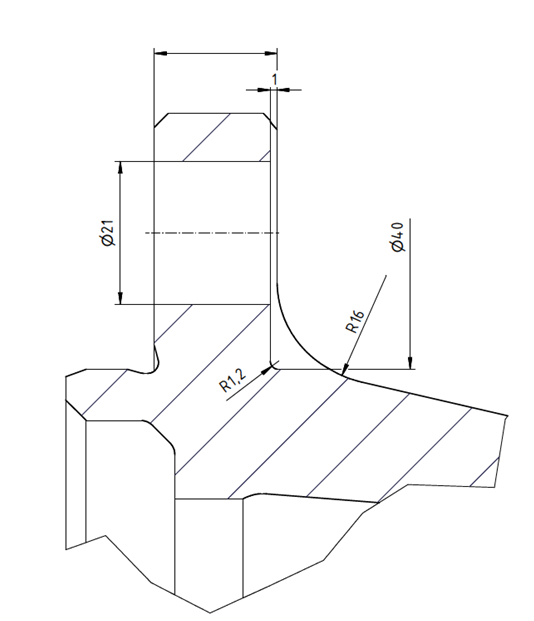
Application Details:
- Bore diameter: Ø21.0 mm
- Countersink diameter: Ø40.0 mm with corner radius R1.2
- Number of bores per workpiece: 40
- Material: G-22 Ni MoCr5-6
- Machine: Lathe Mazak Integrex 70YB / Horizontal machining
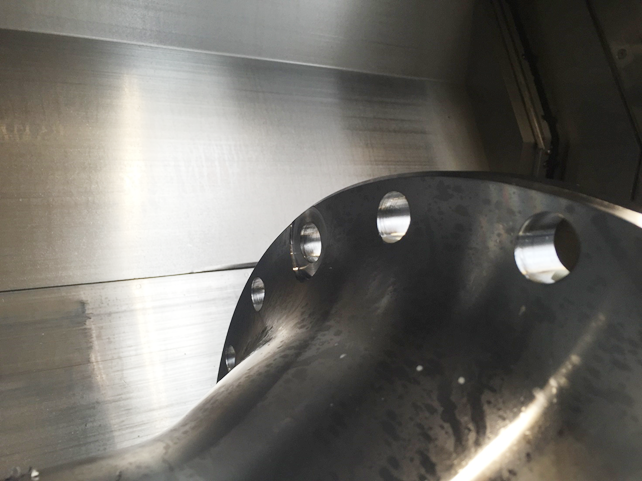
Solution:
HEULE proposed SOLO2. SOLO2 possesses a particular feature: when the spindle is in idle state, the blades are extended. Only at a speed of over approx. 2000 rev/min dp the blades retract. This way, the tool head can travel across the bore to access the back side of the bore. SOLO2 allows low spindle speeds to machine tough materials or interrupted bore edges.
Tool choice: SOLO2 21.0 / 40.0 mm, working length 50 mm
Blade choice: SOLO carbide blade A type coating
Machining parameters:
- Working speed: 300 rev/min.
- Feed: 0.03 mm/rev.

Results:
Of primary importance are the cost savings generated by the complete machining without having to reclamp the workpiece. At a yearly volume of 200 workpieces, automating the back spotfacing resulted in a reduction of over 200 hours, which is still a significant cost saving after accounting for the tool investment. Another benefit to the customer is the elimination of the labor-intensive re-clamping and re-adjustment of the large work piece, which increases efficiency.
Interested in the SOLO back spotfacing tool? Visit the SOLO product page for more info.
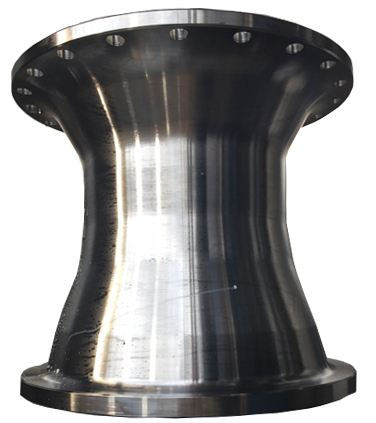
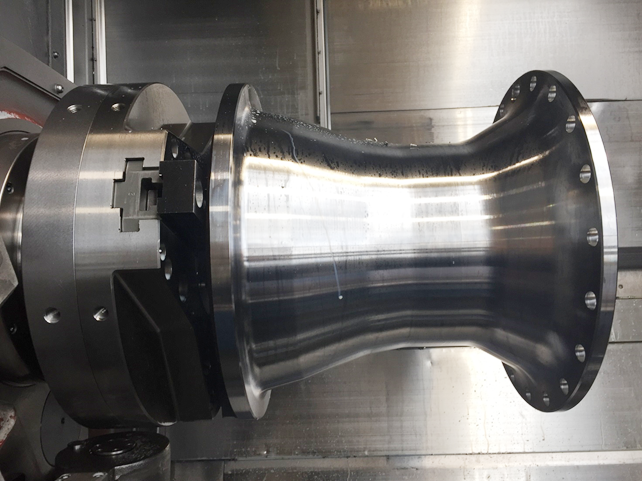